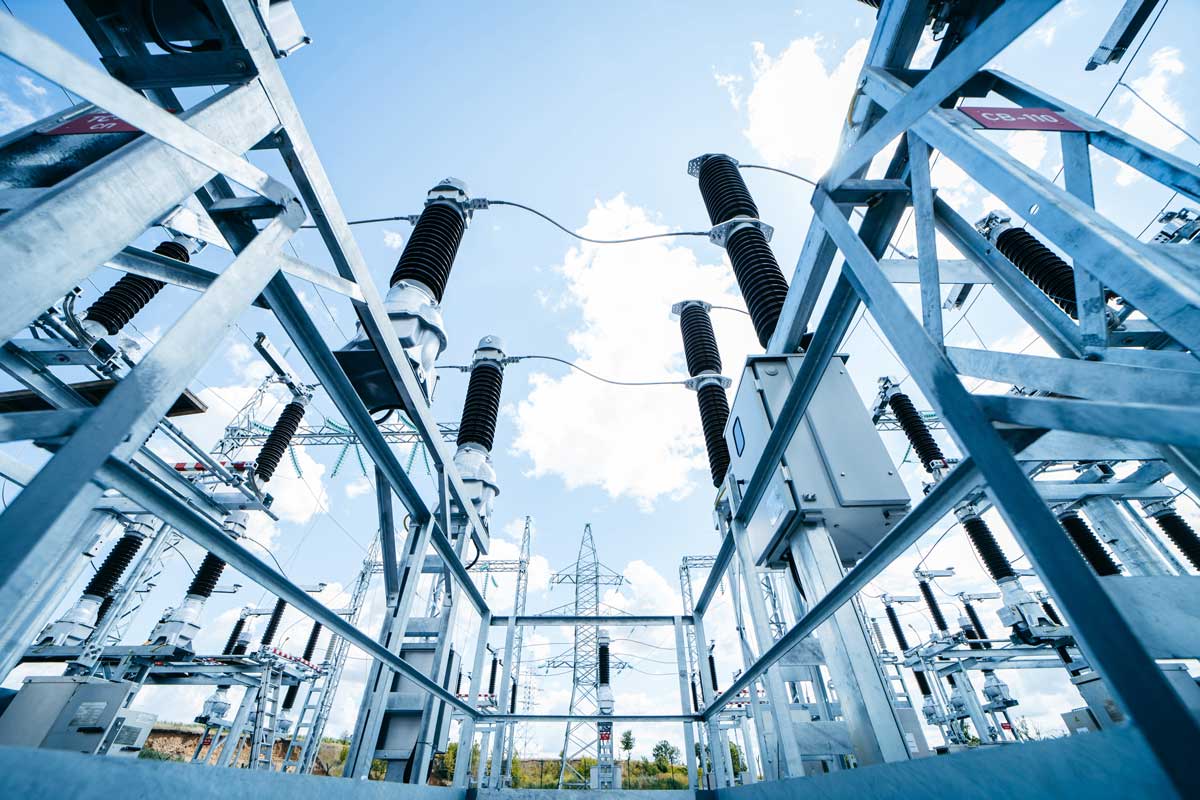
Virtually any industry you can think of is now completely reliant upon electricity. From the public transportation systems used by millions of people every day to the IT, manufacturing, and health care industries, modern life as we know it would not function without a reliable flow of electrical power.
That is why every component of an electrical system is absolutely vital. If one part is not functioning properly, it can bring down the entire system. Today we will look at one component of such systems: connectors. Electrical connectors are devices used to create a connection between various parts of an electrical circuit or to connect multiple circuits together.
Connectors can be used to transmit either power or an electrical signal, and they can work with either AC or DC electricity. In today’s post we are focusing primarily on those used to transmit power.
There are numerous types of connectors available, and it is important to choose the right one for any given application. Regarding installation, they can broadly be broken down into two key categories: compression and mechanical. But what are the differences between compression and mechanical connectors, what advantages does each type offer, and which should you choose for your application?
Understanding Compression Connectors
Compression connectors can be made of either copper or aluminum and can handle voltages ranging from 120V (primarily for residential use) up to 500KV (for utility power transmission applications). The latter are known as extra high voltage connectors.
In a compression connector, the conductor fits into a sleeve made of similar material. Compression then deforms the sleeve in order to make good electrical contact and reinforce strength, ensuring that the conductor does not pull out under normal conditions.
This compression is performed using a crimping tool and a crimping die. Each crimping die is manufactured for a particular wire gauge. Each connector requires a certain number of crimps, which are evenly spaced on either side of the center line. The standard way to perform this process is to begin from the center and then move outward.
Understanding Mechanical Connectors
Mechanical connectors can be made from a range of materials including aluminum and copper alloys. Like compression connectors, they can handle a wide range of cable requirements.
Unlike compression connectors, mechanical connectors do not deform the sleeve into which the wire is inserted. Instead, they operate using screw down points and bolts, which hold the cable inside the mechanical lug. As you turn the screw, it compresses the conductors of the cable to make the electrical connection.
No crimping tools or dies are required for the use of mechanical connectors.
What Are the Key Differences Between Compression and Mechanical Connectors?
Compression and mechanical connectors perform the same basic role and operate in some similar ways. However, there are several key differences in their design, their methods of connection, and the applications for which they are best suited.
All of these factors must be considered as you decide the most appropriate type of connector to use for your application.
Design and structure variations
The main difference in the design and construction of these two types of connectors is that mechanical connectors do not use compression or crimping to secure the connection.
Due to this difference in design, there is a lower chance of the cable accidentally coming loose and falling out of a properly installed compression connector than there is with a mechanical connector. As long as the machine is calibrated correctly, it is easy to ensure a strong, uniform connection.
On the other hand, because custom tools and dies are not required, using mechanical connectors is often faster and easier.
Performance considerations in different conditions and applications
Different connectors are suited to different conditions and applications. Due to the increased risk of the cable coming loose when mechanical connectors are used, compression connectors are better suited to environments with high levels of vibration. In almost all transportation system applications, for example, compression connectors are utilized for this reason.
Mechanical connectors, on the other hand, are ideal in spaces where it would be impossible or impractical to use crimping tools. They are also ideal for applications in which frequent disassembly and reassembly may be required, and for smaller gauge wires and connections.
Cost implications and budget considerations
Using compression connectors comes with an additional cost because of the need for a crimping tool and crimping dies. These items alone can cost several thousand dollars. However, they only need to be purchased once and should last many years with proper care and maintenance.
For mechanical connectors, no additional tools are required apart from a basic Allen key. Mechanical lugs do cost more than their compression counterparts, but the overall cost of using mechanical connectors is lower, unless you are using enough compression connectors to break even when the cost of machinery is taken into account.
Learn More and Get in Touch
Here at MAC, we supply power transmission connectors of a variety of types and for a range of purposes. Our clients range from power utility companies to transportation organizations and more. With more than 50 years of experience, we are one of the U.S.’ most trusted suppliers of quality products for the transmission, distribution, and control of electrical power.
If you would like to learn more about any of our products or any of the information we have covered in this post, please get in touch. Our knowledgeable team members will be happy to assist you by answering your questions and helping you to select the right electrical connectors for your application.
You can contact us via our website contact form, by email, or on the phone.
Related Posts
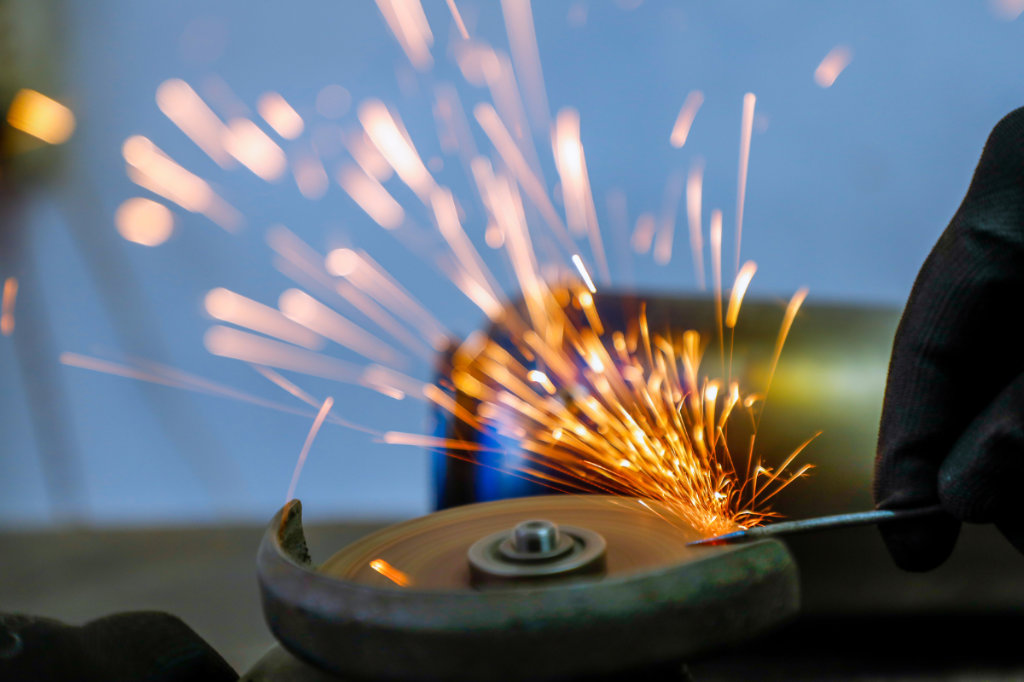
What is the Custom Fabrication Process and Why Is It Crucial for Electrical Utility and Transit Projects?
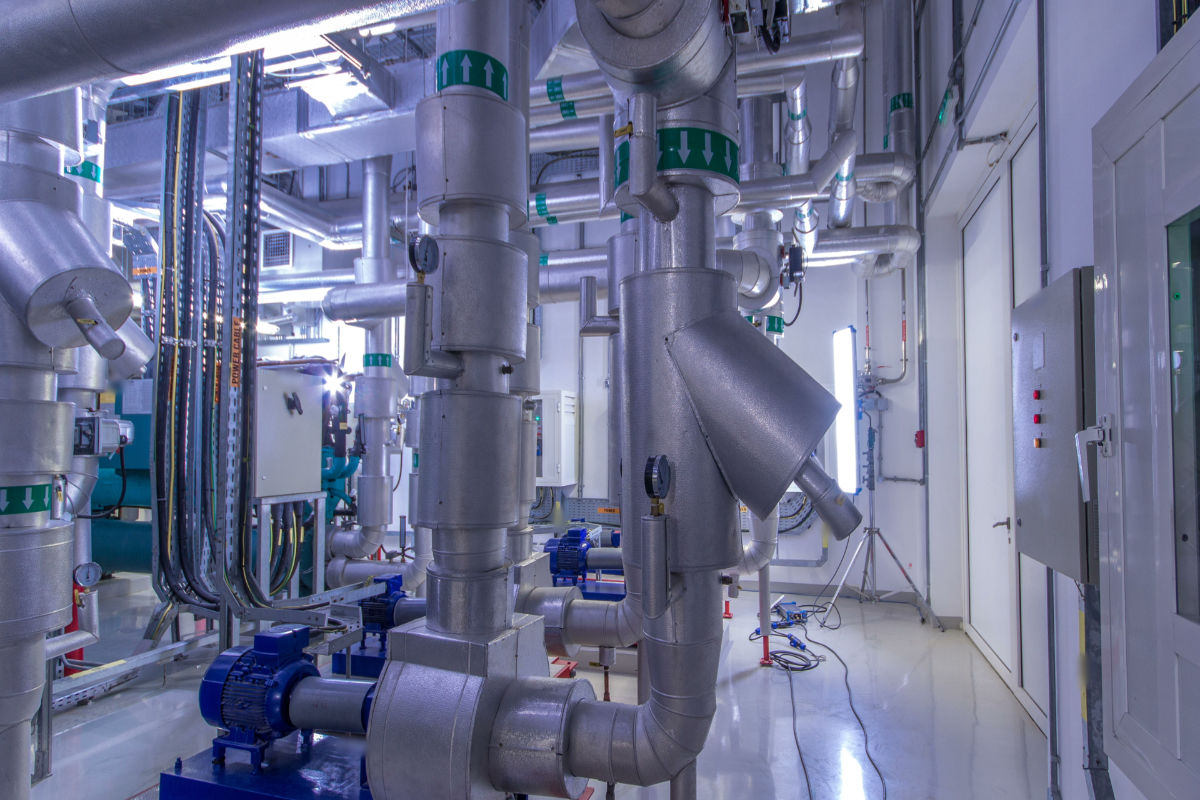
Revolutionizing Cable Cooling: Innovative Solutions for Efficiency and Sustainability in Electrical Utilities
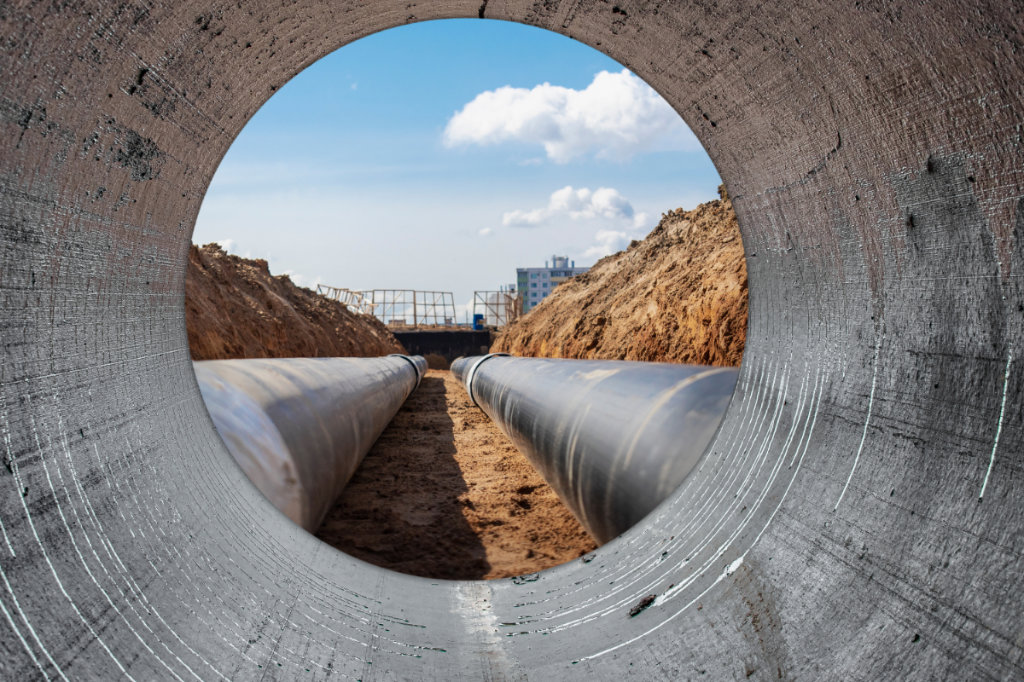